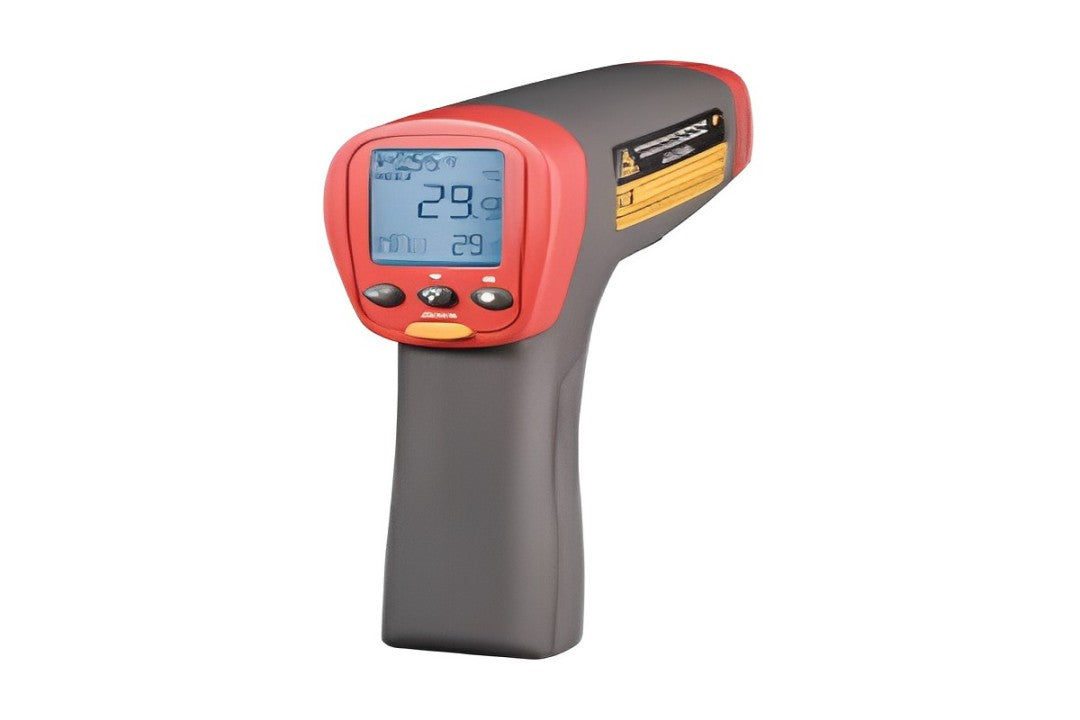
High-Quality Thermometers for Marine Automation Needs
In marine automation, precision and reliability are important. As vessels travel through environments ranging from polar ice to hot tropical seas, accurate temperature monitoring plays a critical role in ensuring peak performance and safety. Thermometers, have an indispensable part to play in marine automation systems. In this blog, we will discuss why high-quality thermometers are vital in marine automation, their types, applications, and how best to choose those that suit your needs.
The Role of Thermometers in Marine Automation
Thermometers are essential in monitoring and controlling various systems aboard a vessel. From engine performance to cargo preservation, temperature data ensures that systems function within safe and efficient parameters. In marine automation, thermometers contribute to:
- Engine Monitoring:
- Ensuring that engines operate within optimal temperature ranges prevents overheating and extends the lifespan of components.
- Monitoring coolant and lubricant temperatures enhances performance and minimizes maintenance needs.
- Cargo Safety:
- For vessels carrying temperature-sensitive goods, such as food or chemicals, precise temperature control is essential to maintain quality and compliance.
- Environmental Control:
- Monitoring seawater and ambient temperatures helps in adjusting HVAC (Heating, Ventilation, and Air Conditioning) systems for crew comfort and equipment protection.
- Energy Efficiency:
- Accurate temperature readings optimize fuel consumption by adjusting systems based on real-time data.
- Safety Systems:
- Thermometers play a role in fire detection and suppression systems by identifying temperature anomalies.
Types of Thermometers Used in Marine Automation
The marine environment demands robust and reliable thermometer solutions capable of withstanding extreme conditions. Here are the most common types:
- Analog Thermometers
- Applications: Frequently used for manual monitoring of less critical systems.
- Advantages: Simple, cost-effective, and durable.
- Limitations: Limited precision and inability to integrate with automation systems.
- Digital Thermometers
- Applications: Widely used in marine automation for real-time data collection and system integration.
- Advantages: High accuracy, ease of integration with digital systems, and user-friendly interfaces.
- Limitations: Requires power and may be vulnerable to electronic interference.
- Infrared Thermometers
- Applications: Useful for non-contact temperature measurements, especially in hazardous areas.
- Advantages: Fast response time and the ability to measure moving or hard-to-reach objects.
- Limitations: Limited to surface temperature readings and can be affected by environmental factors.
- Thermocouples
- Applications: Common in engine rooms and other high-temperature environments.
- Advantages: Wide temperature range, durability, and rapid response.
- Limitations: Requires calibration and specialized knowledge for accurate use.
- Resistance Temperature Detectors (RTDs)
- Applications: Perfect for precise temperature measurements in critical systems.
- Advantages: High accuracy, stability, and compatibility with automation systems.
- Limitations: Higher cost and slower response time compared to thermocouples.
- Bimetallic Thermometers
- Applications: Used for direct temperature readings in less dynamic systems.
- Advantages: Mechanical operation, no power required.
- Limitations: Limited to local, manual readings.
Key Features of High-Quality Marine Thermometers
When selecting thermometers for marine automation, certain features ensure optimal performance:
- Accuracy:
- Precision is crucial, especially for systems that demand tight temperature control.
- Durability:
- Marine thermometers must withstand harsh conditions such as saltwater exposure, high humidity, and temperature extremes.
- Integration:
- Compatibility with existing automation systems, such as PLCs (Programmable Logic Controllers), ensures seamless operation.
- Calibration:
- Regular calibration and ease of recalibration maintain accuracy over time.
- Material:
- Corrosion-resistant materials, such as stainless steel, extend the device's lifespan.
- Response Time:
- Rapid data capture enables timely adjustments and enhances safety.
- Certification:
- Compliance with marine standards like IMO (International Maritime Organization) or DNV (Det Norske Veritas) ensures reliability.
Applications of Thermometers in Marine Automation
Thermometers are integrated into various systems aboard a vessel, ensuring operational efficiency and safety. Key applications include:
- Engine Room Monitoring
- Monitoring coolant, exhaust gas, and oil temperatures ensures the engine operates efficiently.
- Refrigeration Systems
- Accurate temperature control in refrigerated compartments preserves cargo quality.
- Ballast Water Systems
- Temperature monitoring helps comply with ballast water treatment regulations.
- HVAC Systems
- Ensuring crew comfort and maintaining optimal conditions for sensitive equipment.
- Fire Detection
- Detecting temperature spikes in hazardous areas to trigger alarms and suppression systems.
How to Choose the Best Thermometers for Marine Automation?
When selecting thermometers, consider the following factors:
- Application Requirements:
- Identify the specific needs of your system—accuracy, range, and response time.
- Environmental Conditions:
- Choose devices that can withstand the harsh marine environment.
- System Compatibility:
- Ensure integration with existing automation systems.
- Cost vs. Value:
- Invest in high-quality thermometers that offer long-term reliability and performance.
- Maintenance Needs:
- Opt for devices with low maintenance requirements and easy calibration processes.
- Vendor Reputation:
- Purchase from reputable suppliers with expertise in marine-grade equipment.
Innovations in Marine Thermometer Technology
The marine industry has seen advancements in thermometer technology, enhancing their functionality and reliability:
- IoT Integration:
- Smart thermometers equipped with IoT capabilities allow real-time monitoring and remote diagnostics.
- Wireless Thermometers:
- Eliminates wiring complexity and enables flexible installation.
- Enhanced Materials:
- Use of advanced materials for better resistance to corrosion and wear.
- Multi-Sensor Systems:
- Combines various sensors for comprehensive environmental monitoring.
Maintenance Tips for Marine Thermometers
To ensure consistent performance, regular maintenance is essential:
- Regular Cleaning:
- Remove debris and salt deposits to prevent corrosion.
- Periodic Calibration:
- Check and recalibrate thermometers to maintain accuracy.
- Inspect Wiring and Connections:
- Ensure all connections are secure to prevent data loss or inaccuracies.
- Monitor for Damage:
- Replace thermometers showing signs of wear or malfunction.
Conclusion:
Thermometers are essential in taking accurate temperatures across medical, industrial, and environmental applications. Such data may include monitoring health conditions, checking on food safety, optimizing a process, and providing comfort. Now, because of technological progress, thermometers are available from simple mercury-based designs to digital, infrared, and smart devices. The most critical aspect here is the use, as selecting the right type depends on a case-by-case scenario to be assured that the task at hand would not be lessened by lack of reliability or inefficiency.